Ordren som endret ...alt
Hexagon Ragasco er verdensledende innen gassbeholdere av komposittmaterialer – og en av Norges smarteste industribedrifter.
– På det tidspunktet ordren kom inn hadde vi produsert opp to tusen beholdere, så det var litt overveldende for oss. Vi var på mange måter mest bare en forsknings- og utviklingsavdeling på det tidspunktet, snarere enn et ferdig selskap, men så kom det altså inn en ordre på over en halv milliard kroner. Da startet vår reise for alvor, forteller Skjalg Stavheim i Hexagon Ragasco.
Løsningen ble å bygge en helt ny fabrikk, som skulle være fullt automatisert fra første sekund. Det ble en voldsom industribygging: På ett år ble det investert for 150 millioner kroner, og bedriften gikk fra ti til 110 ansatte. Et stort antall roboter og smarte maskiner, digitaliserte rutiner og arbeidsflyter gjorde at hele Statoil-kontrakten ble levert på bare fire år.
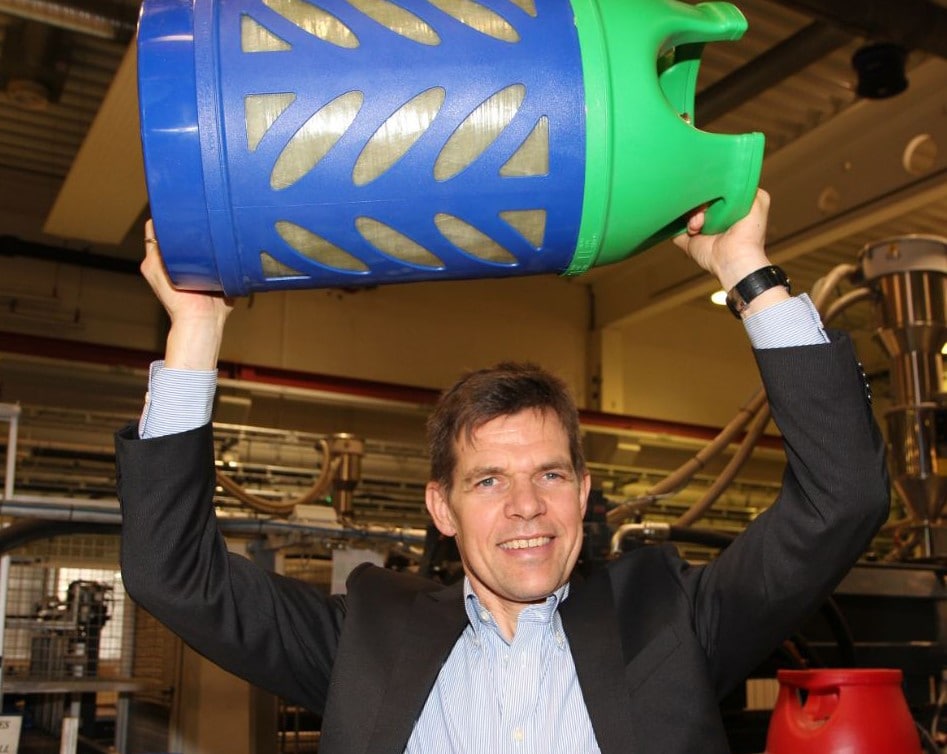
Måtte gå internasjonalt
Med en svært effektiv produksjon skjønte bedriften tidlig at internasjonalisering var nøkkelen for å være liv laga også når den første store avtalen var ferdig. Det viste seg imidlertid vanskelig å få innpass i Europa, selv i land som burde være enkelt sammenliknbare med Norge.
– Tilbakemeldingene vi fikk var at prisene våre var for høye. Et differensiert premiumprodukt med prisvinnende design var ikke nok i seg selv; aller helst burde vi halvere kostnadene. På dette tidspunktet tok det oss ett minutt og fjorten sekunder å produsere opp hver beholder. Vi syntes jo det var ganske bra, og noe vi kunne være litt stolte av, men her måtte vi ta grep. Konklusjonen ble at hvis vi kunne kjøre produksjonen dobbelt så fort med halv bemanning burde det få kostnadene langt nok ned til at vi kunne å få innpass i utenlandske markeder også, forteller Stavheim.
Det var krevende å kostnadsredusere så kraftig, ikke minst fordi det også innebar en del nedbemanning. Til slutt ble prosessen likevel kronet med suksess. Produksjonstiden for en full, ferdig beholder kom ned til 40 sekunder – nesten en halvering – og BP International valgte å inngå en større avtale. Gradvis begynte etterspørselen å øke, og etter nok en radikal ombygging av produksjonen klarte selskapet å få produksjonstiden ned til 20 sekunder for hver ferdige beholder. Stadig flere land meldte sin interesse.
Som treski mot glassfiberski
Siden starten har Hexagon Ragasco jaget produktivitet, syklustider, oppetid og svinn for å holde på konkurransekraften. Produksjonen er seksdoblet, og i dag tar det kun 12 sekunder å fremstille en ferdig komposittbeholder på den fremtidsrettede fabrikken. For neste år har de satt et konkret mål om å redusere dette ytterligere – til bare ti sekunder, fra de opprinnelige 74. Samtidig som produksjonen skal bli mer bærekraftig. Eksporten går til hele 70 land, og dette skal også forbedres.
– Selv med produksjonsveksten vi har fått til har vi bare et par prosent markedsandel globalt, mot de 70-80 millioner stålbeholderne som lages årlig. Men vi håper vår komposittbeholder gradvis kan bli en ny standard. Det blir som treski mot glassfiberski – når du først har prøvd glassfiber går du ikke tilbake!
Et kontinuerlig fokus på å forbedre prosessene, både på fabrikkgulvet og i administrasjonen, er noe av oppskriften på hvordan selskapet skal klare å vokse videre. Bruk av LEAN, automatisering og visualisering av informasjon selv på kontorene nevnes som noen av grepene som tas hver dag for å bli enda raskere. Når du har globale ambisjoner har du ikke tid til å hvile på laurbærene.
Det lønner seg alltid å samarbeide
I 2015 ble Hexagon Ragasco hedret med prisen for Norges Smarteste Industribedrift. Det er ikke så rart: Selv siden før uttrykket «Industri 4.0» kom på banen har selskapet jobbet etter nettopp de prinsippene som ligger til grunn for fremtidens industriproduksjon. Stavheim sier den største fordelen ved kåringen var at de underveis fikk kontakt med andre bedrifter med et tilsvarende fokus på å bli gode, slik at de kunne utveksle erfaringer med dem.
– Det lønner seg alltid å samarbeide for å bli bedre. Det er som når roerne og skigåerne møtes for felles trening. Selv om vi ikke gjør det samme i det daglige er det alltid noen prinsipper som kan utveksles og deles. Så er det også en verdi i å prøve å signalisere at det er mulig å satse selv om man bor i Norge. Det er mye kunnskap og god arbeidskultur her, og norsk industri er konkurransedyktig når den bare gjøres riktig, sier han.
– Det er en fin konkurranse, også fordi det er så viktig at samfunnet får øynene opp for at det er mye moderne som skjer nå. Dagens norske industri består av skjermer, digitale løsninger, visualisering av prosesser, programmering av roboter, fart og ytelse. Det er veldig mye spennende på gang, og du kan være med på å skape noe! Det er noe som inspirerer oss. Industrien har mye godt å by på – og så er det morsomt å kunne innovere så kraftig, avslutter Stavheim.