Smeden som ikke kunne fiske
Det var en gang en sjøsyk unggutt som ville bidra til Sildefisket i Molde på annet vis enn som mannskap på en gyngende båt. Som fingernem smed var han raskt ute med å lage teknologiske nyvinninger for å lette den tøffe, kalde jobben for fiskerne på havet.
Med en sølvmedalje for sine mekaniske garnspill-vinsjer på verdensutstillingen i Paris i år 1900 fikk smeden Nils N. Finnøy blod på tann. Nå ville han lage semi-dieselmotorer til den store flåten med ca 35 fot store fiskebåter. Men det lille verkstedet Nils N. Finnøy Motorfabrikk på Finnøya var ikke stort nok for å lage motorer til alle fiskerne langs kysten – for hvem vil vel ro når det finnes hestekrefter tilgjengelig? Smeden inviterte like så godt alle teknisk interesserte ungdommer hjem til seg for å lære bort å produsere semi-dieselmotorer, og i løpet av kort tid var det hele 35 motorfabrikker i Møre- og Romsdal.
Både Andreas, Anders og Arthur Brunvoll var blant de som gikk i lære på Finnøya, og i 1912 startet brødrene Brunvoll Motorfabrikk. Volda Mekaniske Veksted som Laurits Finnøy i 1913 etablerte som motorfabrikk i Volda etter læretid på Finnøya, er også en del av Brunvoll gruppen i dag. Da markedet for semi-dieselmotorer brått forsvant i 1965 ved de moderne motorenes inntog, fant Brunvoll-brødrene sidepropellere som nytt produktområde. Innmontering av sidepropeller på fiskebåtene skulle løse et gammelt problem når den sprellende silden i nota skulle trekkes inn, nemlig å unngå kollisjon mellom båt og not. Og slik startet suksessen for fjorårets vinner av Norges Smarteste Industribedrift.
«Produsere-i-Norge strategien»
Tilfeldig nok er Odd Tore Finnøy både oldebarnet til den sjøsyke smeden og konsernsjef i Brunvoll AS og Brunvoll gruppen. Han mener den viktigste grunnen til at de ble Norges Smarteste Industribedrift i fjor er det langsiktige eierperspektivet. Konsernet er fortsatt eid 100 prosent av Brunvollfamilien.
– 1992 er et viktig år fordi outsourcingen til lavkostnadsland begynte for alvor. Lederen i Brunvoll på den tiden, Ottar Brunvoll, mente at dette langsomt ville drenere bort kompetansen i selskapet, og definerte derfor en anti-outsourcing strategi. Den heter «produsere-i-Norge strategien», og som navnet tilsier er det akkurat det vi gjør i dag. Dette har vært, og er fortsatt, et langsiktig arbeid som i dag gjenspeiler seg i arbeidet vi gjør med digitalisering, automatisering og robotisering.
Med stort fokus på å bygge kompetanse internt og ikke slippe den ut til leverandører i lavkostland, er Brunvoll stabile i sin posisjon som en av verdens ledende produsenter for propell og thrustersystemer til fremdrift, manøvrering og posisjonering av avanserte skip globalt. Det er «The Brunvoll Way», som den interne produksjonsmetodikken omtales som, er også en stor bidragsyter til.
– Vi har mange pallettbaserte fem-akse maskineringssentre som gjør at et emnet kan bearbeides fra alle kanter. Hele poenget med dette er at du skal spenne opp arbeidsstykket kun én gang, på palettene i maskineringssenteret. På den måten kan operatøren gå hjem klokken 16 mens maskinene jobber videre i to skift til over natten. Dette er vår egen teknologi som vi har utviklet for å klare å konkurrere, og mye av det hadde ikke vært mulig hvis vi hadde fokusert på ett kvartal om gangen, forteller Odd Tore.
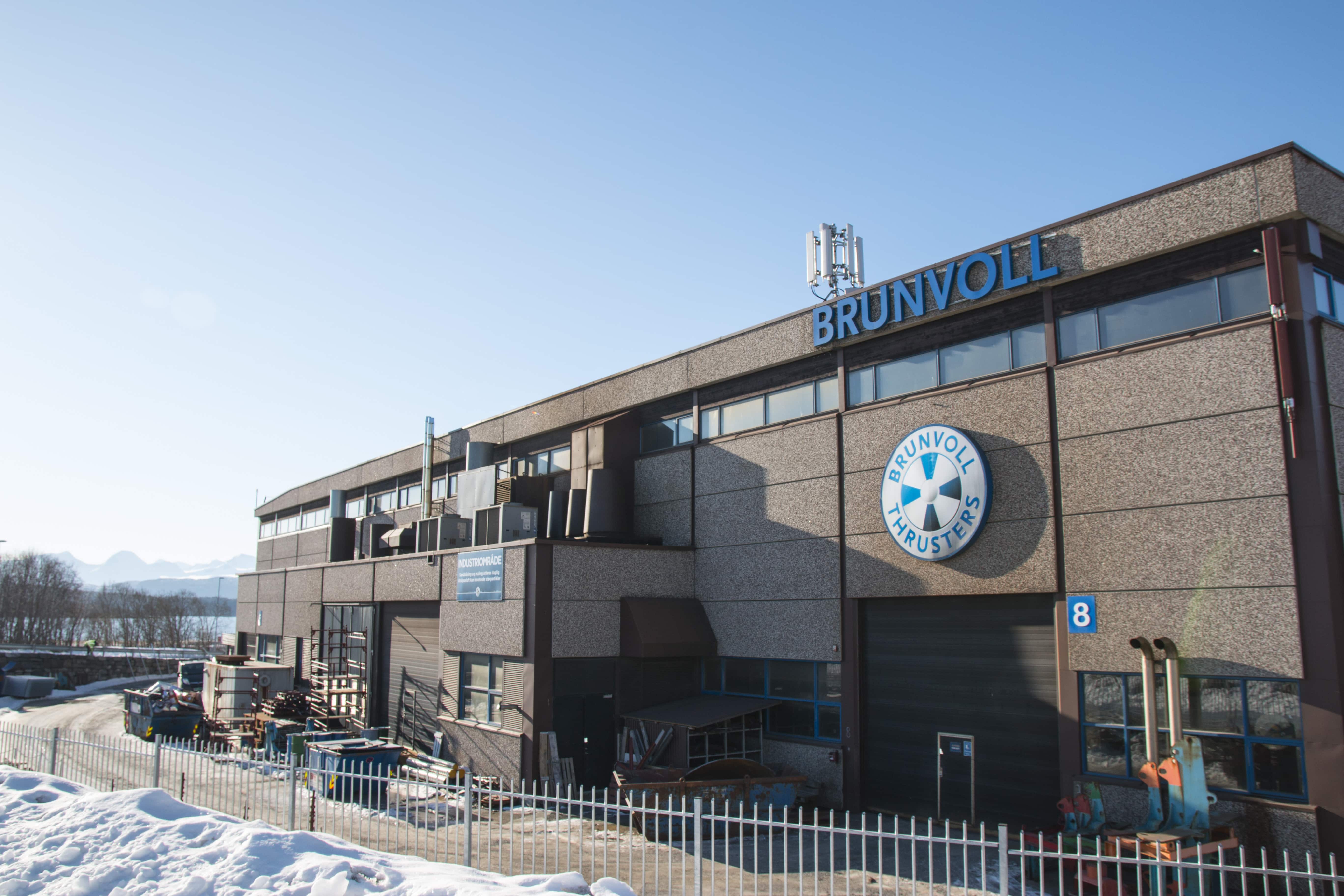
Den røde, digitale tråd
Selv om Brunvoll produserer komponenter det kanskje bare lages én av i året er det nødt til å automatiseres for konkurransedyktighetens skyld. Odd Tore mener dette er grunn nummer to til førsteplassen i fjor.
– Alle våre propell- og thrustersystemer må spesialdesignes, og vi er avhengige av å automatisere på lave volum. For å greie dette har vi utviklet en systematikk der alle data som legges inn fra designfasen, gjennom salgsarbeidet og videre i produksjons- og leveringsfasen og ender opp i våre oppfølgingssystemer i ettermarkedsarbeidet. På denne måten har vi lett tilgjengelig alle data om våre produkt, også hvor alle produkt er installert, når de sist var vedlikeholdt, og hva som eventuelt har skjedd hvis de er utsatt for skade. Det betyr at alle våre administrative system er koblet sammen. Dette kaller vi internt den digitale røde tråden.
Nå har Brunvoll også begynt med maskinlæring og de første maskinene med denne teknologien står og går i dag.
– Hele tiden spør vi oss selv: Hvordan kan vi klare å konkurrere med utlandet? Er vi konkurransedyktige nok nå? Maskinlæring er en følge av dette, og et eksempel er slipe-roboten vår. Den har sensorer som oppfatter hvor slipp pappskiven den sliper med er, og ut i fra dette bestemmer den for eksempel hvor mye trykk den må legge på arbeidsstykket, sier Odd Tore.
Langsiktig kompetansearbeid
«Produsere-i Norge strategien» og dens mål om å holde kompetansen hjemme er noe Odd Tore og resten av Brunvoll priser like høyt i dag som for 26 år siden. Derfor er de stadig rundt omkring til ungdomsskoler og forteller om selskapet, og inviterer også 10. klassinger fra nabokommunene til årlig karrieredag.
– Med de klimautfordringene vi står overfor nå er det viktigere enn noen gang å lage nye løsninger slik at produktene våre blir så bærekraftige som mulig. Det krever enda mer internkompetanse, og det får du ikke kjøpt. Derfor har vi en stor kontingent med lærlinger som viderutvikles som fagarbeidere internt. Dette mener jeg er den tredje grunnen til at vi ble Norges Smarteste Industribedrift. Kompetansebygging er ingen quick-fix, det har vi visst og etterlevd siden 1992, sier Odd Tore.
Godt er det at ikke alle egner seg like godt til havs, og det er utrolig å tenke på at industrieventyret Brunvoll startet med en sjøsyk smed. Med alle sine produkter produsert i Norge og en eksportandel på over 90 prosent, omsetter Brunvoll for over en milliard kroner i året. At de lever opp til fjorårets førsteplass er det ingen tvil om.